|
01Comparison
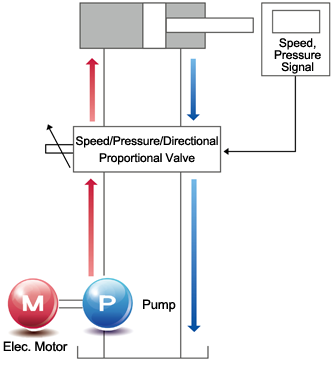
Conventional Hydraulic System
- Command
- Controller ▶Proportional control valve command
- Controller ▶ Pump operation command
- Driving Principle
- Continuous motor and pump operation
- Proportional control valve delivers only necessary flow to the operating mechanism
- The rest of the flow is bypassed (loss)
- Feature
- Motor operating ratio more than 50% under no load condition
- 1200rpm motor, large capacity pump are used
- Electronic proportional control valve response time 80ms or above
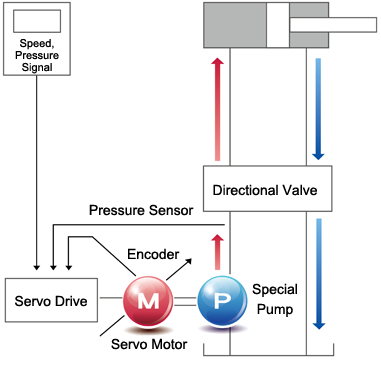
Servo Hybrid Hydraulic System
- Command
- Controller ▶Servo Drive▶Servo Motor▶Pump rotation
- Driving Principle
- Servo Motor and pump make a Optima necessary flow and pressure for operation
- Only Directional control valve controlled the operating mechanism
- Flow and pressure feed-back control
- Feature
- Motor was no operating under no load condition
- 0~2500rpm variable speed control, make a large flow using small displacement pump
- Response time 40ms(simila as Electric Machine)
- Precision machine control using servo system
02Remodeling Procedure
- 01
Machine Diagnosis
- Measure power consumption, examine the specification and performance of the machine to be remodeled
- Refer to technical data (hydraulic & electric circuit drawings
- Work Environment
- 02
Quotation
- Quotation of the servo hybrid system based on the machine specification
- Consult financing
- 03
Agreement
- Discuss and set the delivery terms
- Delivery schedule according to financing method
- 04
Remodeling and commissioning
- Components involved (servo motor, servo drive, servo pump, Hydraulic block, hydraulic piping and electric box)
- No need to edit the program of the existing controller (Use existing electric signals)
- 05
Installation completion report
- Power consumption rate testing
- Training and machine transfer
03Installation details
Mechanical Change
- Servo Motor + Pump
- Manifold (Remove sub plate, valve, etc.)
- Auxiliary pump, if necessary
- Replace hydraulic hose (according to the mechanism and manufacturer)
- Inlet line change
Electrical Change
- Analog output, Additional drive box
- Hydraulic, current / voltage outputs, electric wiring
- SMPS, additional relays, drive signal wiring
- Secure box space (extension card position, additional parts)
04Energy Saving – compare power consumption rate (injection molding machine)
Power Saving with Servo Hybrid System in Injection Molding Machine (up to 75% of saving)
- Save energy by optimizing oil flow and pressure according to the machine operation.
- During holding step, maintain pressure at minimum speed
- During cooling step, no operation, using no energy
05Case Study of Energy Saving
Clamping Force (Ton) |
Clamp Type |
Part Weight (g) |
Cycle Time (sec) |
Before (Kw) |
After (Kw) |
Saving (Kw) |
Saving Ratio (%) |
Savings years (KRW/year) |
L Co. 1300 |
2 PLATE |
1485 |
77.0 |
72.9 |
33.2 |
39.7 |
54.4 |
32,871,600 |
W Co. 900 |
2 PLATE |
781.5 |
72.6 |
64.1 |
29.4 |
34.7 |
54.1 |
28,731,600 |
W Co. 650 |
Toggle |
566 |
58.0 |
50.3 |
20.3 |
30.0 |
59.7 |
24,840,000 |
D Co. 450 |
Toggle |
709 |
50.0 |
46.1 |
20.3 |
25.8 |
56.0 |
21,362,400 |
H Co. 350 |
Toggle |
125.4 |
57.5 |
19.5 |
10.2 |
9.3 |
47.7 |
7,700,400 |
H Co. 250 |
Toggle |
243.1 |
55.7 |
20.1 |
9.2 |
10.9 |
54.2 |
9,025,200 |
H Co. 150 |
Toggle |
155.7 |
49.2 |
13.0 |
5.9 |
7.1 |
54.6 |
5,878,800 |
- Operating Hours : 24 Hrs/day, 25 days/month, 12 months/year
- Power Cost : KRW 115 / KwH
|
|